Granulated Metallurgical Coke
Metallurgical coke is a porous material, which is the most important material
used in a blast furnace, and one of the major uses of this kind of coke is in
metallurgy industries.
Metallurgical coke has various roles in blast furnaces like: energy supply, iron
resuscitation & creating porosity for passage of resuscitative gases.
It should be noted that, this kind of coke is also used in casting, ferroalloys and
as well as steelmaking industries by the method of electric arc furnace.
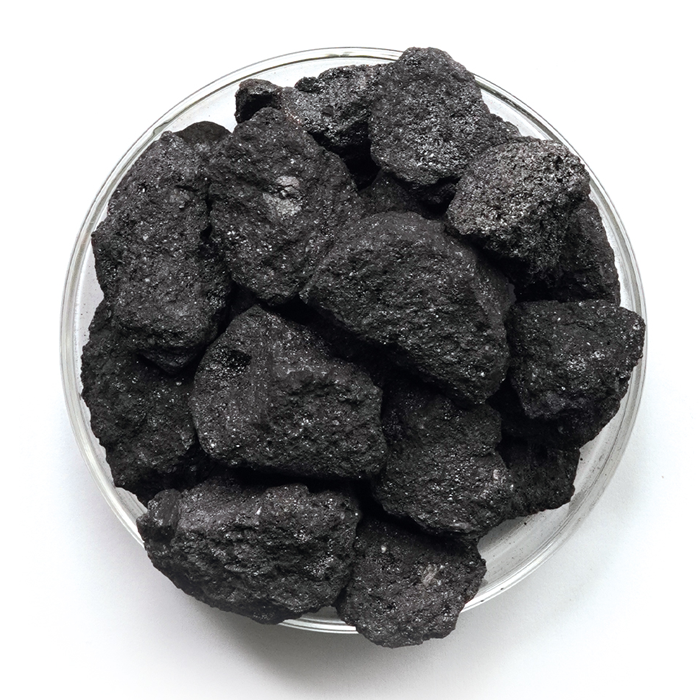
Name | C | ASH | VM | M | S | SIZE |
PSCM80 | 80 | 14-16 | 2-3 | 1-4 | 1/3-1-5 | 60-140 / 25-80 / 25-50 / 15-40 / 5-25 / 1-3 / 0-5 |
Injected graphite
Injected graphite, which is the main product of this company, is the result of the calcination process on raw coke that can be supplied after crushing and grinding operation categorized in 0.5-5, 1-5, 0.5-3, 1-3…
Read More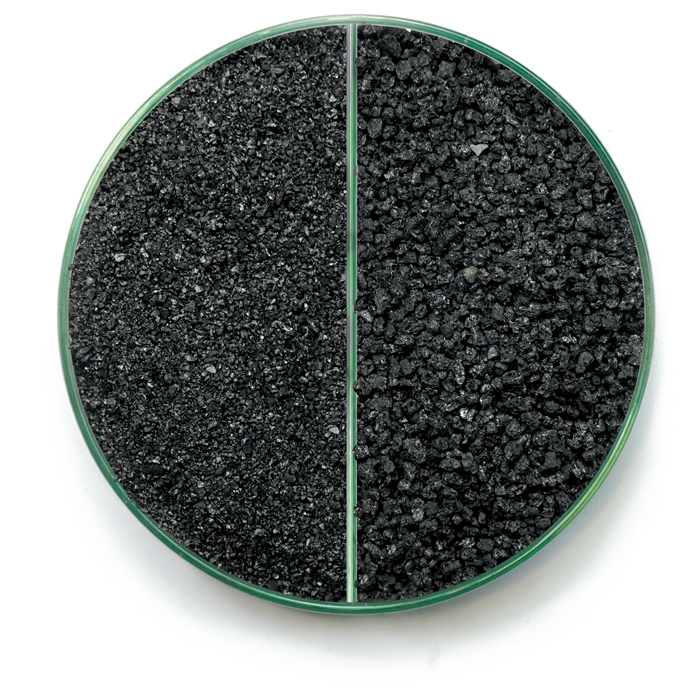
Name | C | ASH | V.M | M | S | Size |
Injected graphite | 97+-1 | 1.5+-0.5 | 1.5+-0.5 | 0/5 | 0/7 | 0.2-1/1-3/1-5 |
Injected graphite | 95+-1 | 3+-0.5 | 1.5+-0.5 | 0/5 | 0/7 | 0.2-1/1-3/1-5 |
Injected graphite | 93+-1 | 5+-0.5 | 1.5+-0.5 | 0.5 | 0.7 | 0.2-1/1-3/1-5 |
Calcined anthracite (injectable):
Anthracite, also known as hard coal, is a hard, compact variety of coal that has a submetallic luster. It has the highest carbon content, the fewest impurities, and the highest energy density of all types of coal and is the highest ranking of coals.
Read More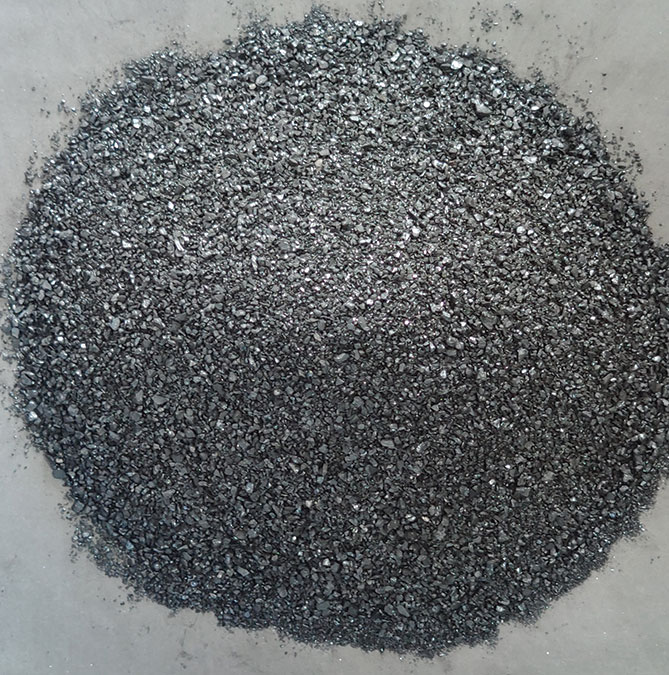
SIZE | S | M | V.M | ASH | C | NAME |
0-0.5 | 1±0.1 | Max 1 | Max 1 | Max 8 | Min 90 | PSC90 |
0.5-3 | 1±0.1 | Max 1 | Max 1 | Max 8 | Min 90 | PSC90 |
0-0.5 | 1±0.1 | Max 1 | 10±2 | 10±2 | 80±2 | PSC80 |
0.5-3 | 1±0.1 | Max 1 | 10±2 | 10±2 | 80±2 | PSC80 |
Coal concentrate briquette
Coal concentrate briquette is the result of the granulation process of fine-grained coke.
Read More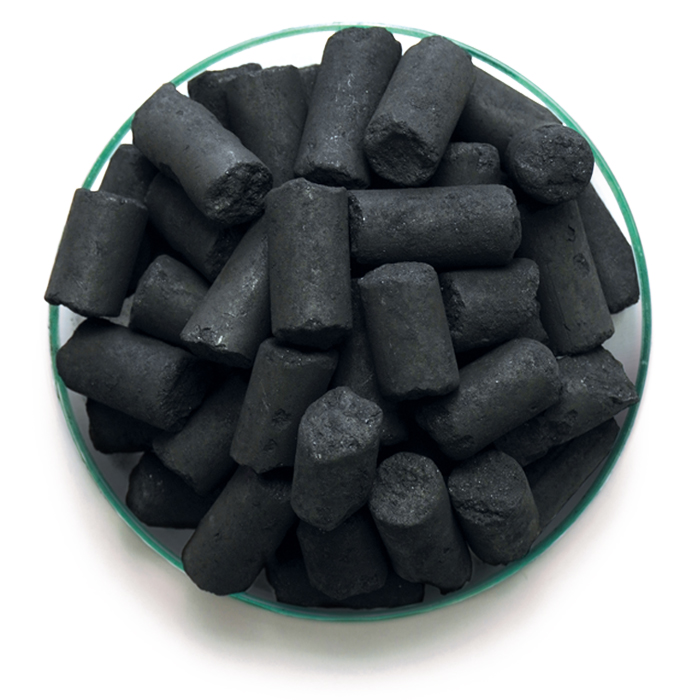
SIZE | S | M | V.M | ASH | C | NAME |
5-15 | 1±0.1 | Max 1 | 12±2 | 8±2 | 80±2 | PSCG80 |
10-30 | 1±0.1 | Max 1 | 12±2 | 8±2 | 80±2 | PSCG80 |
Anti-wear anthracite
As many steel companies tended to use crude anthracite instead of calcined anthracite, after consumption, they realized that the amount of crude anthracite wear for equipment is higher than oil coke and metallurgy.
Now, due to technical knowledge and research in this aspect, Petrosaman Company has started to produce anti-wear anthracite coal.
This product no longer damages industrial devices and equipment due to its anti-wear properties, and it is also not necessary to spend a lot of money to maintain, repair or replace abrasive surfaces.
This can be a vision for the relevant industries so that by consuming this product, they no longer have to worry about the degradability of the equipment and avoid spending a lot of money.
Read More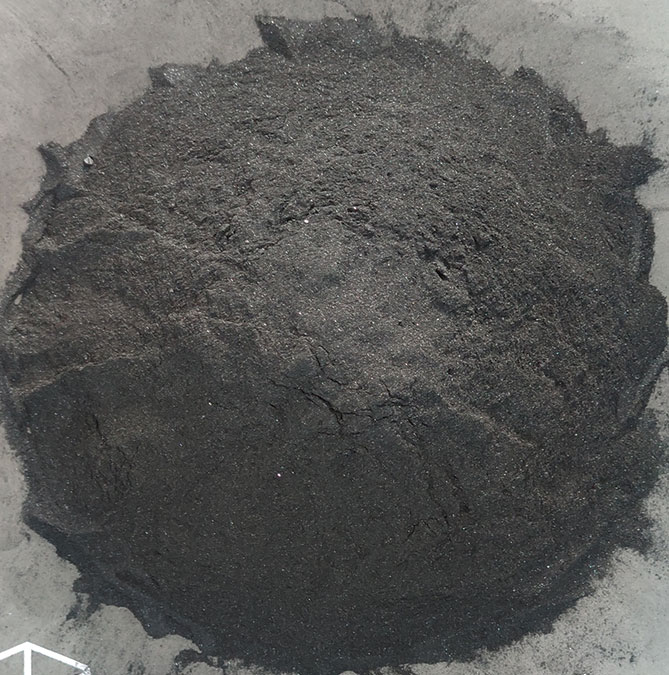
SIZE | S | M | V.M | ASH | C | NAME |
0-1 | 1±0.1 | Max 1 | 12±2 | 8±2 | 80±2 | PSCA80 |
1-3 | 1±0.1 | Max 1 | 12±2 | 8±2 | 80±2 | PSCA80 |
Coal and Concentrate (PCI)
Thermal coal is one of the types of coal and a sub-branch of bituminous coal, which according to its properties and characteristics, it can be used in certain cases.
Thermal coal is divided into two categories, low calorific value coal (LOW CTE) and high calorific value coal (HIGH CTE). The reason for this difference is related to the stages of coal transformation in the earth.
This coal has a lower coking property than coking coal, so it has a more reasonable price.
Basically, the sulfur content of hot coals is less than that of coking coals. It is worth mentioning that sulfur absorbs heat in the form of sulfate when it burns and combines up to 2% of its weight with oxygen and 4% of its weight with water.
Read More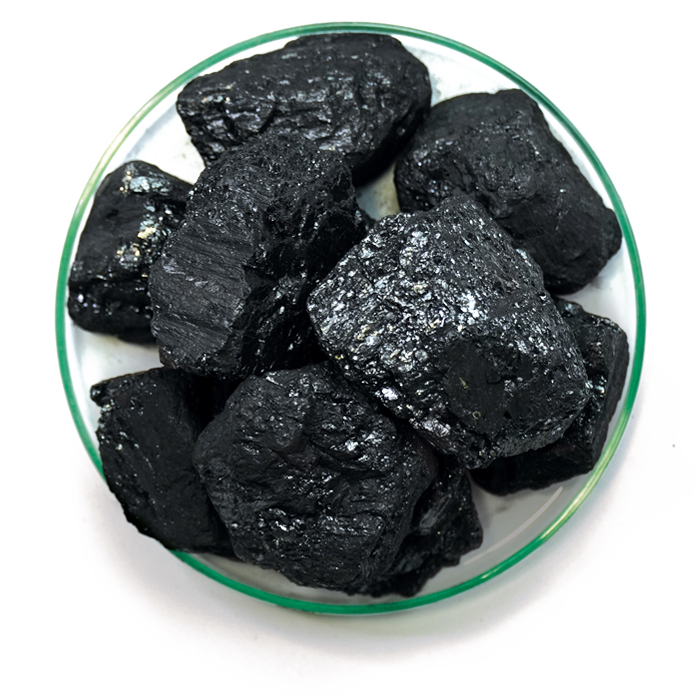
SIZE | S | M | V.M | ASH | C | NAME |
0-37 | 1±0.2 | Max 10 | 10±2 | 10±2 | 80±2 | PCI80 |
0-100 | 1±0.2 | Max 4 | 15±2 | 15±2 | 70±2 | PSC70 |
0-100 | 1±0.2 | Max 4 | 15±2 | 25±2 | 60±2 | PSC60 |
Graphite electrode
According to international standards, graphite electrodes must be made from calcined petroleum coke (CPC). Needle coke production technology, as the main raw material of CPC, is available exclusively to countries such as China, USA, Japan and Germany. This has made the manufacture of graphite electrodes as the main consumable material in electric arc melting furnaces, the monopoly of developed countries.
To produce graphite electrodes, needle coke powder is first molded and compressed with a vibrator. The formed electrode is then baked in an oven. After baking, a layer of bitumen is added to it. Finally, this product is again at a temperature of 3000 degrees Celsius and turns into graphite.
After the production process, turning operations are performed on the electrodes. These electrodes are mostly produced in a cylindrical shape and after production must be cut in standard diameters. It is necessary to install a pin as a socket on the electrode head.
Read More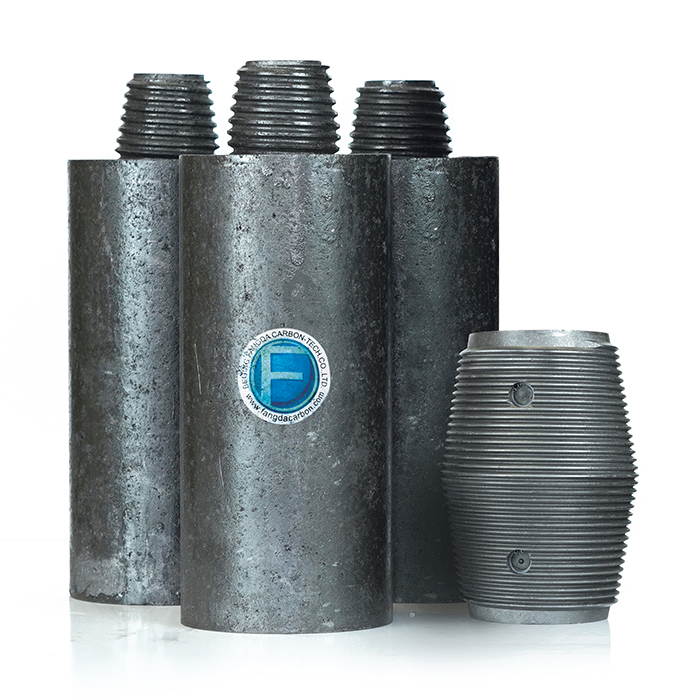
% ASH | CTE 10-6/°C | Modulus of Elasticy Gpa | Bending Strength Mpa | Bulk Density g/cm3 | Resitance µΩ.m | Specification |
0.2≥ | 1.50≥ | 14.0≥ | 10.5≤ | 1.70≤ | 5≥ | Electrode |
0.2≥ | 1.40≥ | 20.0≥ | 20.0≤ | 1.78≤ | 4≥ | Nipple |
Steel sections
Steel sections are produced through processing of raw materials such as slab, steel ingot, bloom and billets, and their carbon content is between 0.16 and 0.25 percent. Among the most widely used and best-selling steel sections, corner, rebar, stud, and beam could be mentioned.
Types and the application of each steel section are different. various sections include many properties and applications in the construction industry, which are produced and developed based on distinct standard methods.
Steel sections are one of the most important building materials which form the structure of a building. They are also used in various industries such as auto manufacturing, shipbuilding, structure construction, etc.
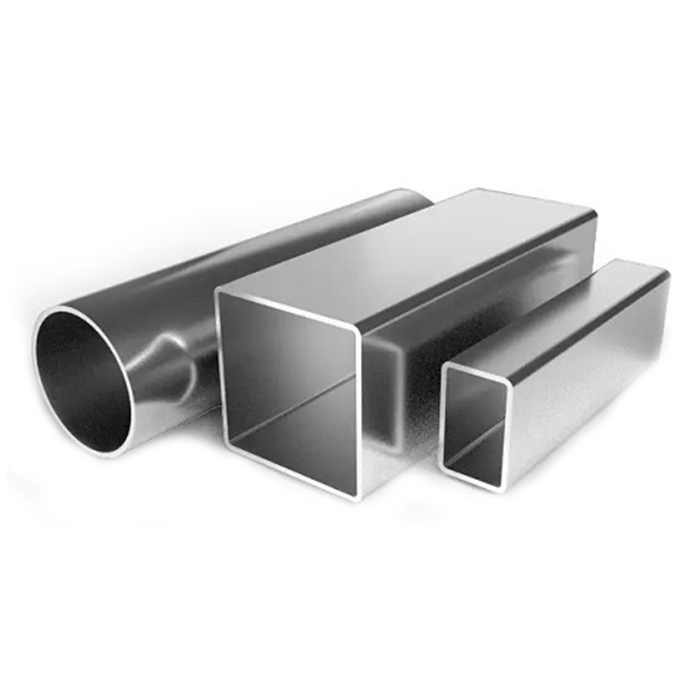
Steel Ingot
Steel ingot is the most important product in the steel production chain. It is the basic material for production of other steel products, having various types which represent unique characteristics and applications.
Steel ingot is the first product made of iron ore, which is the output of steel mill’s production.
Today, steel ingot is the most important product used in steel production chain among which slab, hot Rolled and billet, which are used based on their characteristics, are very popular in the market.
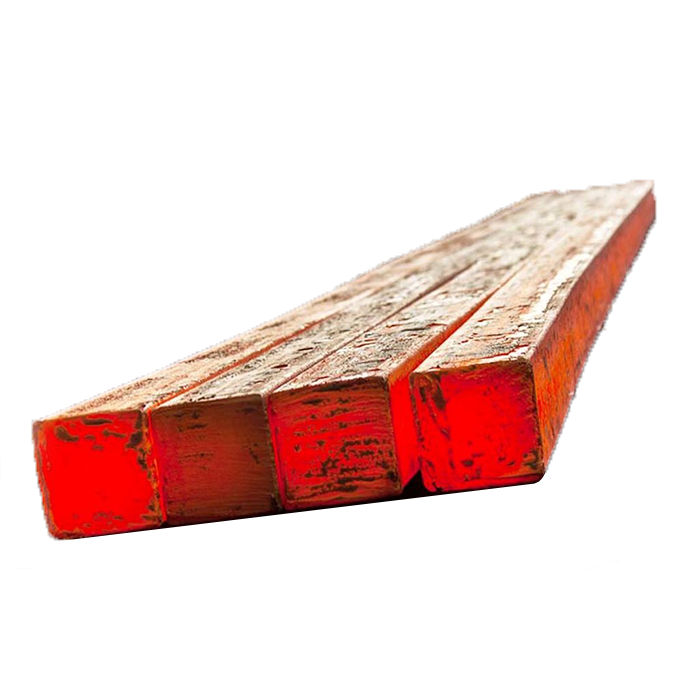
Spong Iron
Direct Reduced Iron (Sponge Iron)
Sponge iron is obtained from the direct reduction of iron ore, and during such operation, its oxygen is removed with no need for melting of iron ore. This product is directly used as a raw material for steel production, especially in electric arc furnaces.
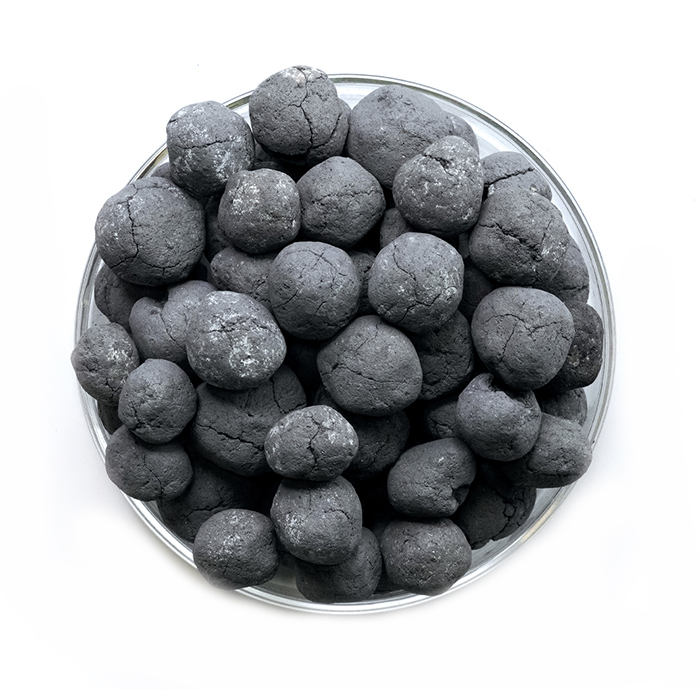
pellet
Pellet is the raw material used to produce pig iron. Its balls are made of iron ore and other baked additives.
The major use of pellets is in the production process of sponge iron, but it is generally used for direct reduction.
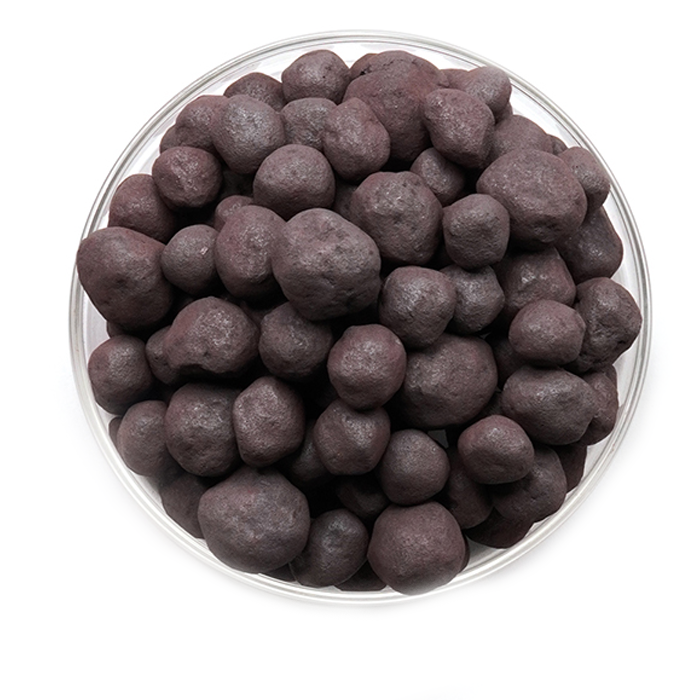
Ferro Alloys
Ferroalloys are among the additives used for melting process, which contain a significant percentage of elements such as manganese, aluminum, silicon, chromium, etc., and are used to create special and unique properties in steel and metals.
Among the applications of ferroalloys, de-oxygenation, alloying, nucleation in iron casting, etc., could be mentioned, which alloying is considered as the most important of one.
Currently, various ferroalloys are produced throughout the world, and Petro Saman Company supplies various types of ferroalloys regarding customer requests, which the most important are as below:
All types of ferromanganese, all types of ferrochrome, ferrosilicomanganese, ferrosilicon, ferrophosphorus, ferromolybdenum.
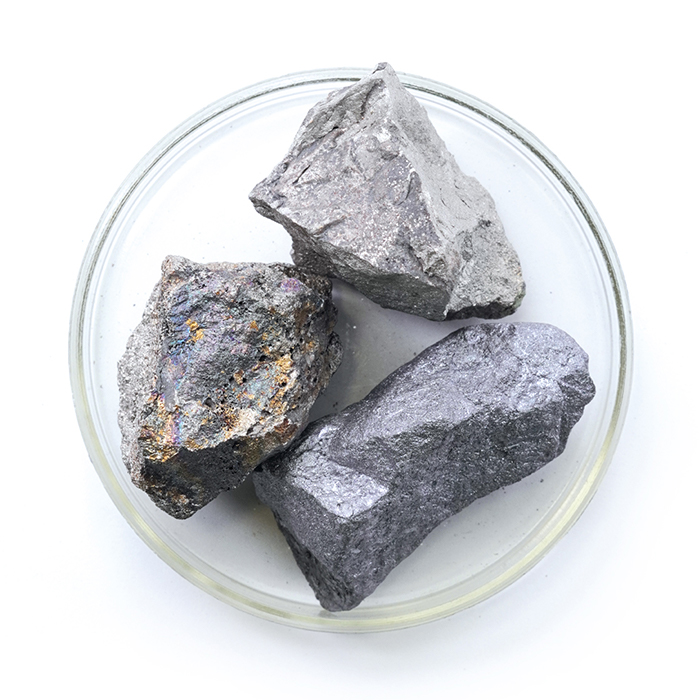